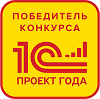


- Комплексное управление ресурсами предприятия (ERP)
- Оперативное управление производством (MES)

Цели проекта
Основными целями проекта являлись разработка и внедрение импортонезависимой системы оперативного управления производством MES на базе отечественной платформы 1С и ее интеграция в общую информационную среду Заказчика в крайне короткий срок.
Изначально заказчик поставил перед нами задачу по сохранению функциональности существующей зарубежной системы. Однако благодаря экспертизе нашей команды и открытой и активной позиции клиента, мы смогли трансформировать запрос в работы по качественной перестройке системы управления производством и созданию уникальной системы MES.
Ситуация до внедрения
Группа компаний ITMS — один из лидеров российской табачной отрасли.
Портфолио компании включает международные и российские марки сигарет: Dunhill, Kent, Vogue, Rothmans, Lucky Strike и Ява, а также альтернативную инновационную продукцию – системы нагревания табака glo и одноразовые электронные испарители Vuse. Фабрика компании в Санкт-Петербурге считается одним из лучших производств России с точки зрения соблюдения ESG-принципов: почти 100% мусора перерабатывается, более 40% воды используется повторно.
В связи с локализацией бизнеса и отключением от глобальных систем возникли риски прекращения работы системы управления производством, которые далее могли вылиться в полную остановку или существенное снижение производительности выпуска готовой продукции.
Для организации технологической автономности производства Клиент инициировал проект по переносу функциональности на российское ИТ-решение.
Уникальность и инновационность проекта
Отсутствие коробочных решений MES для покрытия требуемого функционала управления производством:Система на 90% является кастомной, поддерживающей уникальные особенности производственных процессов. За основу была взята конфигурация "1С:ERP. Управление холдингом", которая была выбрана в качестве учетной системы Заказчика, что позволило уменьшить сложность интеграции между системами.
Работа производства 24/7:
Фабрика работает в режиме 24/7. Для обновлений и регламентных работ удалось выделить в сутках два окна по 20 минут с наименьшей пользовательской активностью в моменты чистки оборудования.
В силу особенностей проекта отказались от подготовки больших релизов. После проверок на тестовом контуре, задача внедряется в продуктивный.
В период активной разработки система обновлялась почти ежедневно.
Вовлеченное участие команды Заказчика:Для реализации проекта со стороны Заказчика была выделена отдельная команда. Три самых напряженных месяца разработки вместе ежедневно (без выходных), непосредственно на производстве. Получился довольно сложный, но интересный и главное эффективный процесс, который позволил запуститься за короткий срок.
Сжатые сроки проекта:В связи с комплексной ИТ-трансформацией полностью менялась сетевая инфраструктура. Старт полноценной разработки – март 2023. К этому времени относительно стабилизировался шаблон ERP, от которого можно было отталкиваться. 1 июня началась опытно-промышленная эксплуатация MES. Соответственно, на полноценную разработку было 3 месяца в режиме постоянных изменений.
Публикации о проекте
Дополнительная информация к описанию проекта
Дополнительный экономический эффект - снижение стоимости поддержки ИС.
Результаты проекта
Для Заказчика была разработана качественно новая система управления производством. Созданное решение расширило функционал, по сравнению с исторической системой, и объединило те системы компании, которые ранее не были связаны между собой. На предприятии также налажены информационные потоки и прослеживаемость изготовления продукции, а также обеспечен процесс поддержка бесперебойной работы производства.
-
Оригинальная разработка на платформе 1С:Предприятие
:
- Нормативно-справочная информация
- Диспетчеризация производства
- Цеховой складской учет
- Контроль качества
- Отчеты и аналитика
- Администрирование и настройка
- Обмен данными
- FAQ
-
1С:ERP. Управление холдингом
Архитектура решения и масштаб проекта
Часть данных загружается из учетной системы ERP, а часть ведется или дозаполняется в MES. В подсистеме хранится вся основная информация, связанная с номенклатурой и ее составом, технологией производства, структурой производственных мощностей и другая информация, которая является основной для управления производственным процессом.
Работа с производственными заданиями (ПЗ)
- Подготовка ПЗ. Получение ПЗ из ERP с данными о выпускаемой продукции (включая плановые сроки изготовления, артикул, количество, серию и ресурсную спецификацию). MES автоматически подбирает соответствующую маршрутную карту по подразделению и виду изделия, создает производственные операции по рабочим центрам.
- Обеспечение производства. Заказ материалов на линию и общие места хранения в цехе напрямую с логистического склада или через буферные склады.
- Валидация материалов. Проверка материалов на соответствие спецификации или наличие разрешения на добавление сверх спецификации, соответствие сроков годности. Валидация происходит посредством ТСД. Запрет на старт ПЗ без прохождения валидации.
- Смена сорта. Процесс перехода с одного ПЗ на другое: проверка возможности завершения текущего и старта нового ПЗ, сверка материалов и характеристик продукции.
- Выполнение ПЗ. Контроль выполнения производства, регистрация отходов и промежуточного выпуска.
- Выпуск продукции и полуфабрикатов в зависимости от настроек подразделений (по весу, по паллетам, по коробам и паллетам). Получение данных о выпуске из внешних систем. Фиксация фактического расхода материалов с учетом провалидированных серий материалов.
Управление цеховой логистикой
- Ведение топологии складов в цехе. Система позволяет задать структуру производственных складов (включая ячеистое хранение), контролировать хранение ТМЦ в зависимости от установленных настроек (общие зоны, типы ячеек, сроков годности и т.д.), мониторить и контролировать состояние запасов в цехе с учетом текущего плана производства.
- Проведение инвентаризации в производстве. Блокировка складов/движений на время проведения инвентаризации. Настройка правил проведения инвентаризации. Анализ фактического потребления материалов с учетом scrap.
- Перемещение товаров между складами. Настройка правил оформления документов перемещения, контроль сроков годности материалов в цехе, прослеживаемость ТМЦ в разрезе паллет и ячеек. Создание заказов на перемещение для логистики (отгрузка в производство, возврат из производства, поступление из производства). Отражение перемещения между производственными складами.
- Настройка НСИ. Ведение справочников измеряемых параметров продукции, в т.ч. формулы расчета допустимых граничных значений. Настройка правил применимости инспекционных планов: для продукции, линий, подразделений.
- Формирование актов. Регистрация некачественной продукции (инвентаризация, подтверждение контролером, обработка производством, закрытие аналитиком). Регистрация некачественных материалов. Блокировка стока.
- Контроль параметров продукции. Учет валидации и калибровки оборудования. По полученным с измерительных приборов данным построение графиков качества, на которых выведены:
- Среднее значение каждого набора измерений;
- Детальная расшифровка по каждому набору образцов;
- Среднеквадратичное отклонение по каждому набору;
- Допустимые интервалы значений.
Обмен данными
- Подсистема предоставляет инструменты для проведения обмена данными с внешними системами.


































































































